Atritor Sustainability Journey to Zero Energy by 2025
We have our SHAPA (Solids Handling and Processing Association) Sustainability Award 2023 proudly displayed on our reception desk.
Here’s the film that we submitted to tell our story to date on reducing our carbon emissions from energy. It also gives details of the steps we intend to take to become net zero from energy by 2025.
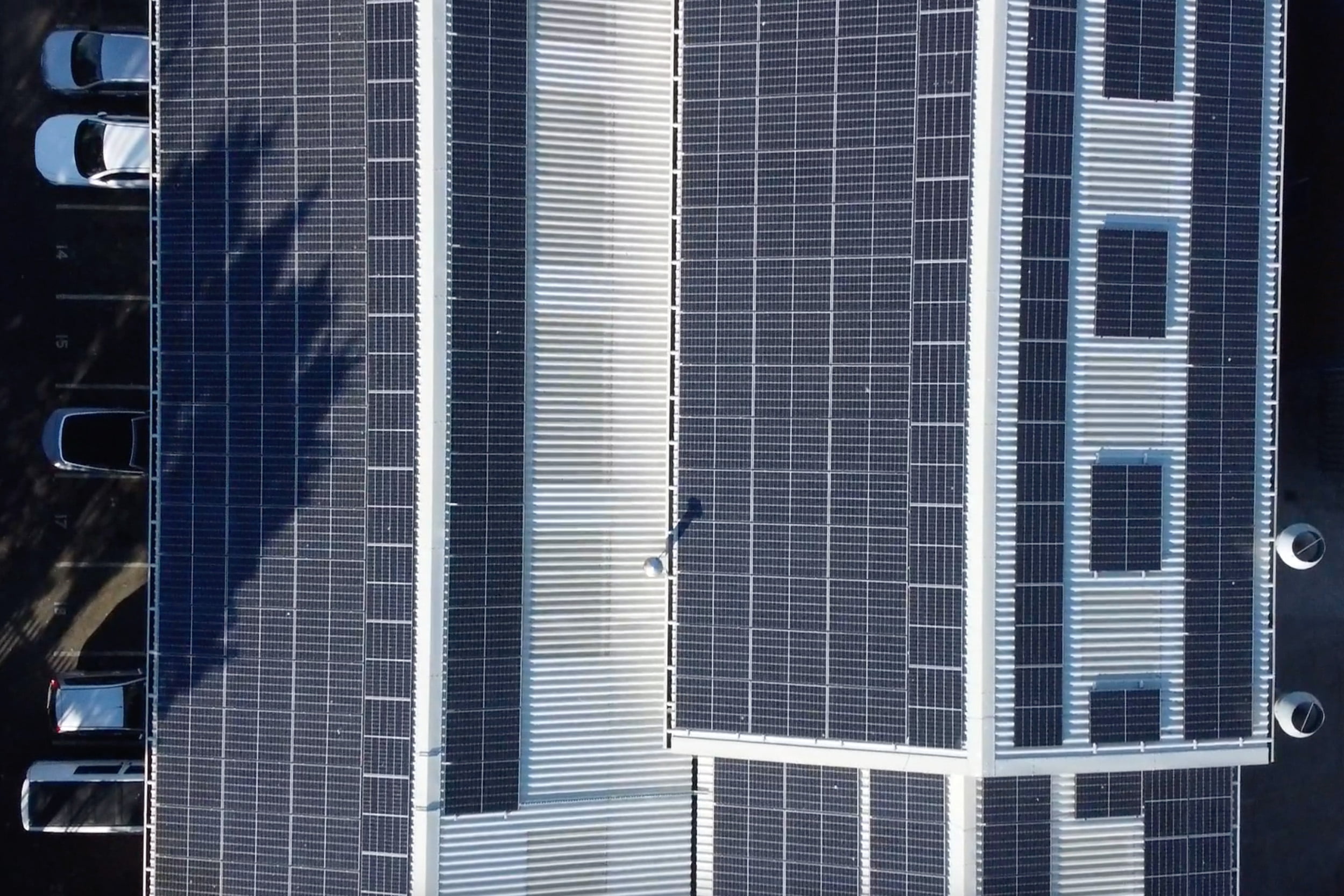
Video transcript
Atritor is on a journey to net zero energy usage by 2025. We’d like to share our story so far. Our sustainability goals are:
- To reduce carbon and stabilise operating costs, so that we continue to provide high-quality products are competitive prices.
- To reduce the environmental impact of our business and improve sustainability.
- To reassure our customers that we are a responsible organisation.
The Atritor journey to net zero energy usage so far…
Solar has more than offset our electricity usage
- We have installed 970 panels, 345kW Solar array on the roof at our site in Coventry, England.
- We also have 60KWh battery storage.
- And air source heat pumps providing the heat for our office.
- We produce 325MWh of electricity that provides more than 100% of our electricity usage for our manufacturing facility, including our foundry and offices, and provide a net export to the grid of over 100MWh per year. This will later be used to provide 400MWh per year of heat through heat pumps to heat our manufacturing facility.
We’ve added to our Solar array, and now we have just under 1000 panes installed.
Our gas usage has reduced by ⅔ in 10 years.
- We have installed a heat management system which has reduced gas usage from its 1.2GWh a year to 750MWh a year.
- We have significantly improved building insulation to reduce our consumption further to 420MWh a year.
We operate fully electric and hybrid company vehicles.
- Electric charging points are installed on-site and powered by the Solar array.
We recycle metals for making components in-house.
- Of the 120 tonnes of meat fed into the foundry, more than 90% is from recycled sources.
- All the iron used in our foundry comes from old railway track.
- Wear parts returned by our customers are recycled.
From April to October, we expect to have a net export of over 100MWh to the grid. We are exporting more energy than we use to the grid.
What’s next?
- Improving insulation in the few remaining older parts of our facility.
- Installing heat pumps to remove gas space heathers from our manufacturing facility.
- Converting our changing facilities and showers to electric heat pumps.
- Wherever we can, we will reduce our carbon impact, and for the minority of our business that unavoidably generates, like essential business air travel, we will buy carbon offsets.
We also help our customers to lower their carbon emissions from energy.
The process we design and manufacture for our customers can be operated using waste heat, significantly reducing energy requirements.
Where waste heat is not available, we include heat recovery from the process.
Our sustainability journey isn’t over yet, but we are well on our way to our target to become net zero energy use by 2025.