Food milling
As a pivotal process in the food industry, food milling enhances the bioavailability and digestibility of various products by reducing larger food grains and ingredients into finer particles. The primary and secondary reduction of these substances, followed by additional grinding to reach the desired size, results in an increase in the surface area of food particles, which promotes better absorption during consumption.
Food milling process
This process is integral to a wide array of sectors within the food industry, including the dietary and nutritional supplement sector, pet food manufacturing, and the burgeoning edible insect market.
Milling dietary and nutritional supplements
In the rapidly evolving supplements sector, food milling is key to achieving precise particle size for improved dissolution rates, texture, and taste. The efficient bioavailability of supplements, often consumed in pill or powder form, relies heavily on the fineness of particles. Milling processes help in producing supplements with consistent particle size distribution, contributing to quality and customer satisfaction.
Pet food milling
The pet food industry also leverages food milling extensively. The process contributes to producing nutrient-dense pet food with desired texture and digestibility. Pet food often incorporates diverse ingredients, including meats, grains, and vegetables. Milling these to the right particle size helps ensure uniform mixing, improved palatability, and optimal nutrient absorption for pets.
Edible Insects
An emerging sector gaining rapid popularity due to sustainability and nutritional factors is the insect-based food industry. Edible insects are milled into a fine powder that can be used as a protein-rich ingredient in various food products, from protein bars to pasta. The milling process is particularly vital in this sector, as it helps to eliminate any psychological barriers associated with consuming insects, transforming them into a more consumer-friendly ingredient.
With extensive experience in designing and building industrial food milling machines, we appreciate the solutions needed to boost efficiency, reduce energy costs, and increase yields for our clients. Effective food milling unlocks the full nutritional potential of our food, underscoring its importance in various food industries.
Specifying a process for food milling
The process we undertake when designing a solution for industrial food milling involves a number of important considerations, such as:
- Raw material: The nature and characteristics of the food to be milled will significantly impact the process design. For instance, the moisture content, hardness, fat content, size, and shape of the food determine the type of mill to be used and the milling conditions.
- End product specification: The required attributes of the end product, such as particle size distribution, texture, and appearance, will greatly influence the milling process. For example, some applications may require a fine powder, while others may need larger, more uniform particles.
- Process efficiency: The efficiency of the milling process is an important consideration. This includes both energy efficiency (minimising the energy required for milling) and yield efficiency (maximising the amount of usable product).
- Scalability: Food milling process design also takes into account increases or decreases in production volume as demand changes.
- Regulatory compliance: Food milling processes comply with relevant food safety regulations, such as those set by the FSA or equivalent bodies in other countries. This could involve using food-grade materials and adhering to regulations on allergen control, labelling, etc.
- Equipment selection and maintenance: The milling equipment needs to be durable and reliable. Plans should be made for regular maintenance to prevent breakdowns and ensure consistent product quality.
- Environmental considerations: The milling process should be designed to minimise environmental impacts. This could involve reducing energy use, minimising waste, and considering the life cycle impacts of the equipment.
- Economic factors: Cost is always a crucial consideration. This includes both the initial outlay for the equipment and the ongoing operational costs, such as energy, maintenance, and labour.
- Worker safety: The design of the food milling process always considers the safety of both the operators and the equipment. This includes considerations like dust control, noise control, and ergonomics. Good design can reduce the risk of accidents and equipment damage.
Materials we work with
Atritor machines can handle a wide range of food materials, each with unique characteristics and processing needs. These include cereals, pulses, and seeds, as well as calcium-rich food sources and fibre-rich ingredients. Our capabilities also extend to hard grains, proteins, vitamins, and minerals. We also work with various types of pet food materials.
Beyond these, our food milling expertise is vast. With over 90 years of experience, we have data on thousands of tests on over 500 categories of materials, giving us the technical expertise to design and build solutions suitable to diverse food processing needs.
Food milling with Atritor
Our cutting-edge industrial food milling solutions are designed to meet a variety of processing needs. We offer solutions for dry milling, fine milling, deagglomeration, and classifying food materials, allowing efficient processing and optimal product quality. Our machinery is built for precision and durability, ensuring consistent performance even in the most challenging milling operations.
Our expertise in milling food allows us to cater to the unique requirements of the industry. Atritor machines are designed and built to deliver optimal results and ensure very high-quality output for clients.
Atritor solutions simultaneously dry and mill materials from 95% moisture to less than 0.01%.
- The Cell Mill is ideal for super fine milling of chemical products.
- The Dryer-Pulveriser is used for coarser materials that are harder or more abrasive.
- The Microniser is particularly suitable for small-capacity applications.
Our experts work closely with clients to understand the application and identify specific requirements. Get in touch with our team to discuss your food processing challenge and see how we can help you.
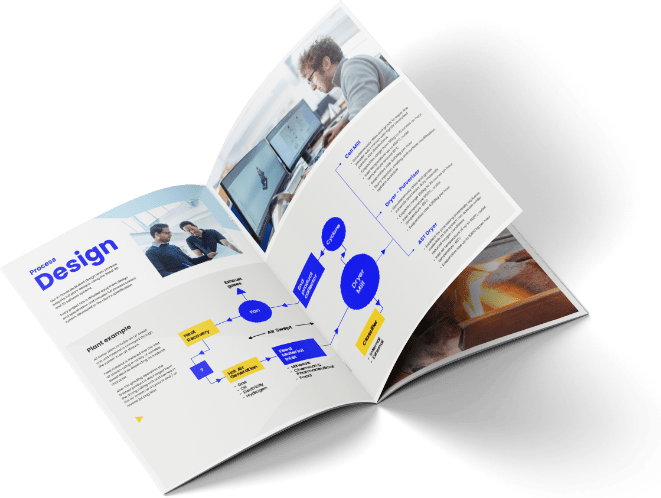
Solving materials processing challenges
Download to learn more