Pharmaceutical milling
Pharmaceutical milling, an essential operation in pharmaceutical manufacturing, involves breaking down active pharmaceutical ingredients and excipients into finer particles. This process commences with primary and secondary size reduction of pharmaceutical materials, reducing them to smaller parts. The final stage of grinding turns these particles into ultra-fine powders through a pharmaceutical mill.
Using pharmaceutical milling to augment the surface area of particles improves their dissolution rate, thereby enhancing drug bioavailability. Atritor pharmaceutical milling equipment ensures optimal milling, promoting increased efficiency, reduced energy consumption, and superior yields. Essentially, effective pharmaceutical milling is instrumental in unlocking the full therapeutic potential of drugs, rendering it a vital process in the pharmaceutical industry.
Specifying a process for pharmaceutical milling
The process we undertake when designing a solution for industrial pharmaceutical milling involves a number of important considerations, such as:
- Material characteristics: Each pharmaceutical substance has unique properties, such as hardness, abrasiveness, chemical composition, and moisture content. The milling process needs to be tailored to handle these different characteristics effectively.
- Desired particle size: The milling process needs to achieve the correct particle size, as this affects the bioavailability of the drug. This often involves several stages of size reduction, from coarse grinding to ultra-fine milling.
- Energy consumption: The milling process needs to be designed to minimise energy consumption, which contributes to overall production costs.
- Product quality: The milling process must ensure optimal product quality, ensuring that the final pharmaceutical product meets the required standards for safety and efficacy. This includes considerations of purity and consistency of the milled products.
- Scalability: The milling process should be designed with scalability in mind, being able to handle both small and large-scale production volumes.
- Compliance: The milling process needs to be designed in compliance with pharmaceutical industry regulations, such as those set out by the MHRA and EMA.
- Process versatility: Given the wide range of pharmaceutical materials, the process should be versatile enough to accommodate various dosage forms.
- Process integration: The milling process should be designed to integrate smoothly with other processes in the pharmaceutical production line, such as drying, deagglomeration, and classifying.
- Process control and monitoring: To guarantee optimal operation and quality assurance, the procedure should have robust control and monitoring systems in place.
- Maintenance and durability: The milling equipment needs to be durable and designed for easy maintenance to avoid frequent breakdowns that can disrupt the manufacturing process.
Materials we work with
Atritor machines handle a broad spectrum of pharmaceutical materials, each with unique characteristics and processing requirements. This includes a range of APIs, excipients, and other formulation ingredients, along with various pharmaceutical-grade compounds. Our capabilities extend to hard pharmaceutical substances, complex chemical compounds, and vitamins. We also work with versatile pharmaceutical materials used in various dosage forms. Beyond these, our expertise in pharmaceutical milling is extensive, making our services comprehensive and adaptable to diverse pharmaceutical manufacturing needs.
With knowledge gained over 90 years and data on thousands of tests on over 500 categories of material, we are able to build bespoke solutions that provide high-quality products for our clients. Whatever your process challenge, we have the technical expertise to help. Read more about the process we use to develop bespoke solutions for our clients here.
Pharmaceutical milling with Atritor
Atritor machines provide clients with advanced pharmaceutical milling equipment that caters to a variety of processing needs. We design solutions for dry milling, fine milling, deagglomeration, and classifying pharmaceutical materials, enabling efficient processing and optimal product quality. Atritor machines are constructed for precision and durability, ensuring steady performance even in the most challenging milling operations.
Atritor solutions simultaneously dry and mill materials from 95% moisture to less than 0.01%.
- The Cell Mill is ideal for super fine milling of chemical products.
- The Dryer-Pulveriser is used for coarser materials that are harder or more abrasive.
- The Microniser is particularly suitable for small-capacity applications.
Our project teams work with clients to identify requirements and understand the application. Get in touch to discuss your pharmaceutical processing challenge or idea and see how we can help.
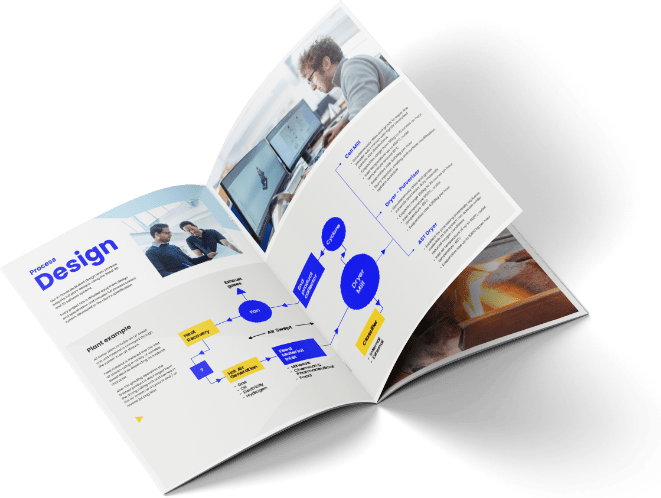
Solving materials processing challenges
Download to learn more